

外径30μm以上の
1ミクロンオーダーにも対応!
“特殊小径ピン.COM”は「プレス加工では生産ができない」、「切削加工でも量産ができない」など、これまで技術面から不可能、あるいはコスト面から実用不可能と思われていた、数多くの特殊小径ピンの試作生産、量産生産を実現してきています。
私たちが手掛ける特殊小径ピンは、外径φ6mm以下のサイズでCNC旋盤、外径φ12mm以下のサイズで複合加工機を用いて、ミクロン精度を実現しております。また、1ミクロンオーダーの形状・精度を要求されることも少なくなく、“特殊小径ピン.COM”では外径30μm以上において、1ミクロンオーダーにて特殊小径ピンならびに周辺部品を製作することができます。
このような形状・精度での特殊小径ピンの製作は、単に加工機械設備を整えるだけでは実現は不可能です。そのために、“特殊小径ピン.COM”は、あらゆる加工設備や加工工具・加工法を日々見直しながら、技術の追求を行い続けています。

ピンの先端加工や穴あけ加工に対応!
“特殊小径ピン.COM”では、ピンの先端加工や穴あけ加工に対応しています。ピンの先端加工においては、CNC旋盤を用いて、外径0.05mm以上のサイズのものに対してフライス加工で4ツ山を加工することができます。また、穴あけ加工では、複合加工機を用いて加工しています。これらの加工は、ピンが小径であればあるほど、変形(反り)やバリが発生しやすく、さらにワークが小さいためバリ取りを行うことも難しくなります。そのため、“特殊小径ピン.COM”では、最適条件(加工プロセス・加工速度・工具選定)で加工することで、変形(反り)やバリの発生をゼロに近づけています。
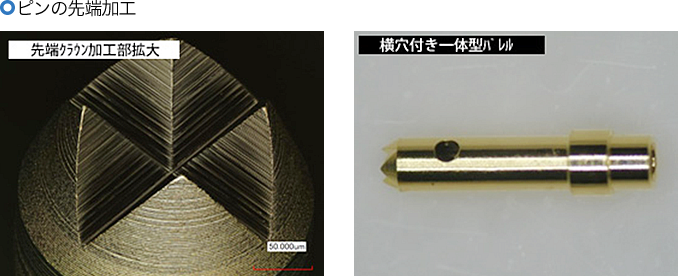
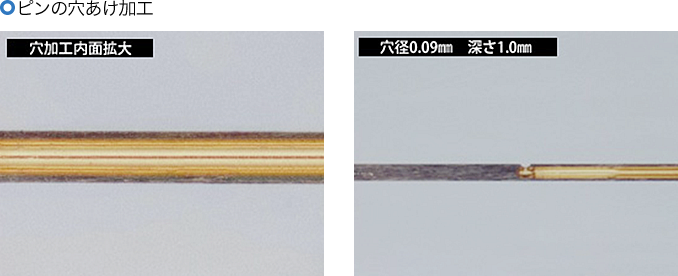

特殊ピンを
試作から100万本まで対応!
“特殊小径ピン.COM”では、100台以上のCNC旋盤を保有しており24時間稼動しています。さらに、量産だけでなく試作(1個~)を随時行える体制も整えておりますので、お客様の試作から量産、量産から市場投入までの開発リードタイムの短縮に取り組んでいます。また、“特殊小径ピン.COM”では、量産を見据えた試作を最も得意としており、初期の設計段階から量産性を追求した技術提案(VA/VE提案)を行っています。
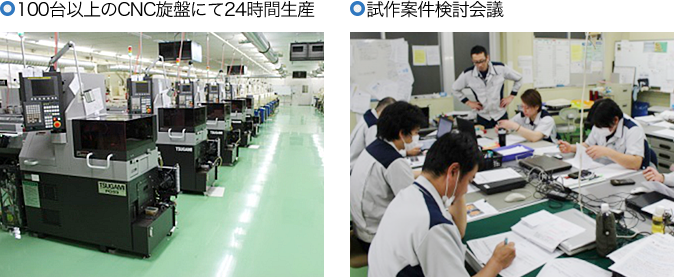

クリーンルーム内での各種組立に対応!
“特殊小径ピン.COM”では、クリーンルーム(クラス100,000)内での組立に対応しています。小径ピンのような微細部品同士を組み立てる場合、小さな埃などの僅かな不純物が不良につながります。そのため、静電気、温湿度、ほこり対策の施されたクリーンルームにて良質の製品を組立しています。組立製品の例としては、、以下のようなものがあります。“特殊小径ピン.COM”が今までに組立を行ったパイプの最小外径はφ0.1mmです。さらなる、小径の組立にも挑戦中です。
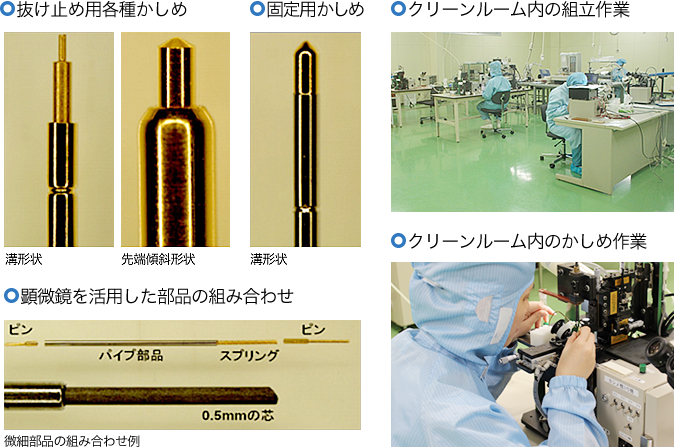

穴あけ治具製作やピン挿入まで対応!
“特殊小径ピン.COM”では、穴あけ治具の製作及びピン挿入まで対応しています。特殊小径ピンは単体で使用される場合と治具に固定して使用される場合があります。この穴あけ治具は、数百個の小穴(穴径φ40μm~)があいている樹脂製となります。使用用途は小径ピンの固定になります。“特殊小径ピン.COM”では、小径ピン・穴あけ治具の製作からピン挿入(組立)まで一貫対応しております。具体的な製品として、コンタクトプローブピンがあり、複数のコンタクトプローブピンを穴あけ治具に挿入したものが半導体通電検査用ソケットとなります。
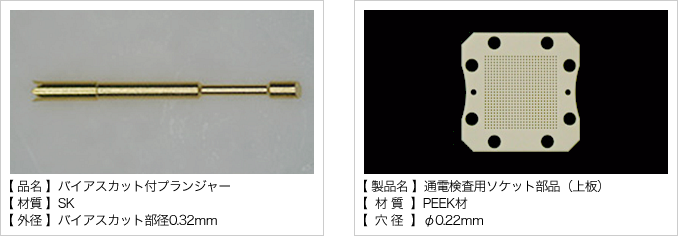

「 荷重・抵抗・耐久・非破壊 」
検査等に対応!
“特殊小径ピン.COM”では、特殊小径ピン及びピン周辺部品の「 荷重・抵抗・耐久・非破壊 」 検査等に対応しています。寸法管理の他、組立時に、荷重検査・抵抗検査・耐久検査・非破壊検査を実施しています。また、組立受託、検査受託(試料郵送または試料持込み、立会い可能)サービスを行っております。
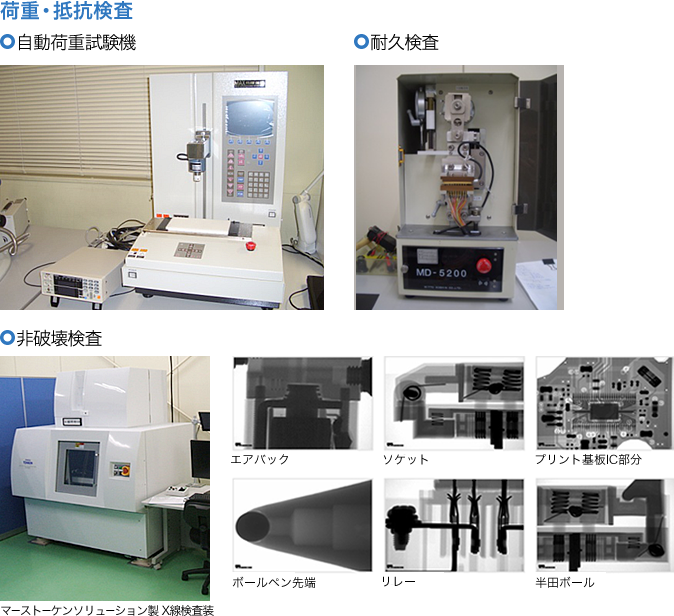

現物からのスケッチ・
図面起こしにも対応!
お客様が今使用している小径ピンやピン周辺部品において、改良改善が必要ではありませんか?
“特殊小径ピン.COM”では、お客様がお持ちになっている小径ピンやピン周辺部品をお預かりして、スケッチや図面起こしを行っております。 また、単にスケッチ・図面起こしをするだけではなく、よりコストダウンにつながるVA/VE提案もさせていただきます。例えば、ピンの先端がつぶれやすいので改善を行う、ピンと周辺部品の摺動性を高められるよう形状変更や材質・表面処理の変更を行うなどが挙げられます。
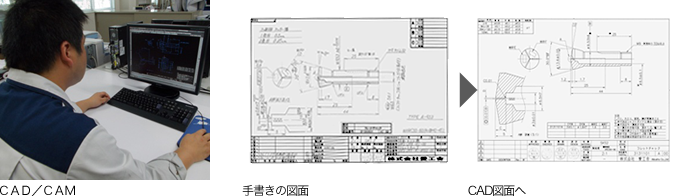


- 1.【新着情報】穴加工において形状変更によるコストダウンのポイント②
- 2.【新着情報】ポケット加工において形状変更によるコストダウンのポイント④
- 3.外形角部において設計変更によるコストダウンのポイント①
- 4.ポケット加工において形状変更によるコストダウンのポイント③
- 5.ポケット加工において形状変更によるコストダウンのポイント②
- 6.ポケット加工において形状変更によるコストダウンのポイント①
- 7.座ぐり加工において形状変更によるコストダウンのポイント
- 8.タップ加工において形状変更によるコストダウンのポイント②
- 9.タップ加工において形状変更によるコストダウンのポイント①
- 10.穴口元のテーパー形状において形状変更によるコストダウンのポイント
- 11.段穴加工において形状変更によるコストダウンのポイント
- 12.穴加工において形状変更によるコストダウンのポイント①
- 13.外形角部において設計変更によるコストダウンのポイント②

- 1.非磁性環境においてコンタクトプローブの材質変更による品質向上のポイント
- 2.耐熱環境下においてスプリングの材質変更による品質向上のポイント
- 3.パイプ(バレル)加工において材質変更による品質向上のポイント
- 4.バレルのめっき処理において形状変更による品質向上のポイント
- 5.バレルの加工において形状変更による品質向上のポイント
- 6.パイプ(バレル)おいて材質変更による品質向上のポイント
- 7.バレルのかしめにおいて寸法指示の緩和によるコストダウンのポイント
- 8.バレルのかしめにおいてリング形状の位置変更による品質向上のポイント
- 9.プランジャーの先端部分において形状変更による品質向上のポイント
- 10.プローブの組立において部品点数削減によるコストダウンのポイント
- 11.圧入が必要なASSY品において一括発注によるコストダウンのポイント